Turn Information into Intelligence
Connect Libelium IoT Gateway with analytics, operations and decision support systems for smart outcomes.
Recognized as an Emerging iPaaS and Hybrid Integration Platform (HIP) Provider by Gartner, Forrester, and MarketsandMarkets.
Turn Information into Intelligence
Connect Libelium IoT Gateway with analytics, operations and decision support systems for smart outcomes.
Recognized as an Emerging iPaaS and Hybrid Integration Platform (HIP) Provider by Gartner, Forrester, and MarketsandMarkets.
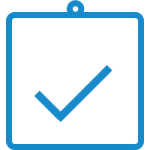
Reduce costs and improve operations by building event-driven workflows with IoT data feeds.
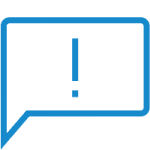
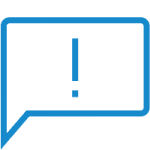
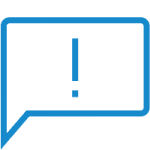
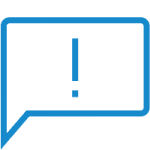
Respond quickly to events, incidents and environmental changes with the power of real-time data.
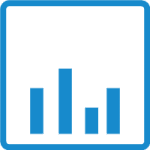
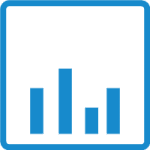
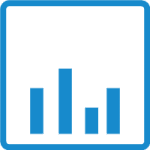
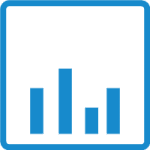
Collect analytics for strategic decision making and build a statistical model for a proactive response.
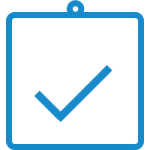
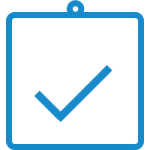
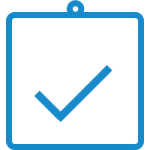
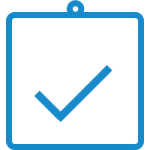
Reduce costs and improve operations by building event-driven workflows with IoT data feeds.
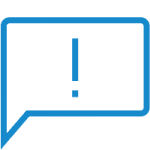
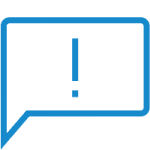
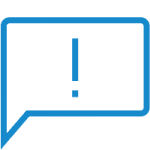
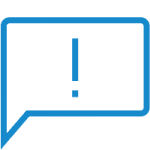
Respond quickly to events, incidents and environmental changes with the power of real-time data.
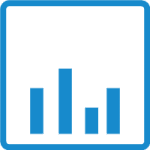
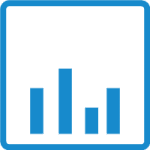
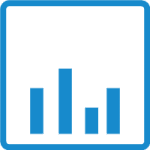
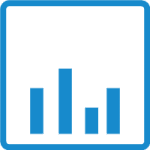
Collect analytics for strategic decision making and build a statistical model for a proactive response.
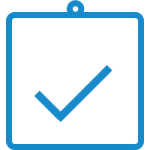
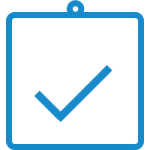
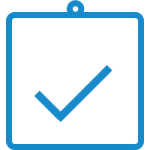
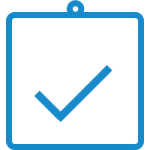
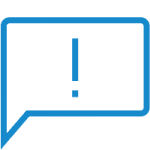
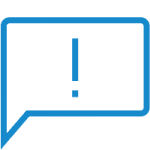
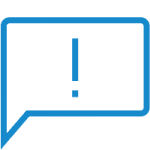
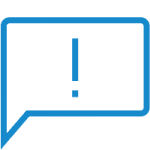
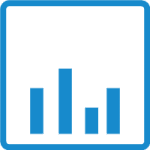
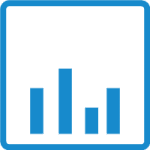
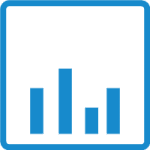
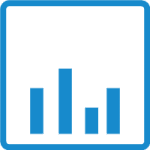
Reduce Costs
Faster Incident Response
Improved Analytics
Not sure where to start? Check out Libelium use case videos
Connect PagerDuty with Libelium for increased visibility of any issues reported by your IoT sensors or devices. In just a few minutes you’ll be set to receive automatic PagerDuty alerts when a sensor returns abnormal data.
Use Connect iPaaS to automatically create incidents in ServiceNow in response to any abnormal data returned by IoT sensors or devices. Decrease response time by integrating Libelium with your incident response platform.
Checkout Libelium API and data connectors on Connect iPaaS
Libelium Use Cases
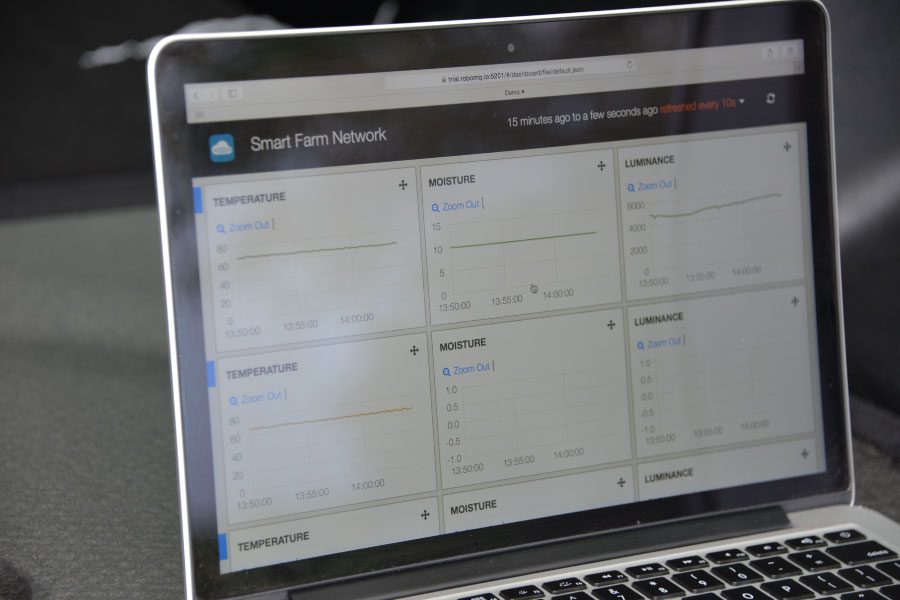
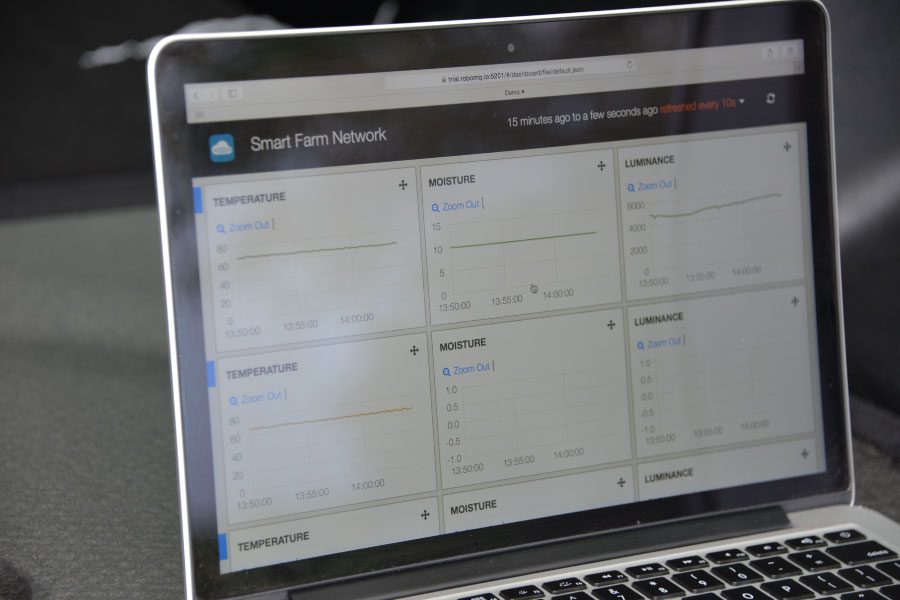
Farmers Leverage IoT Technology to Manage Crops and Controls for Climate Challenges
Without granular data for predictive analytics, it is difficult to know how variable elements have impacted the physiology of the grape. The grape’s weaknesses cannot be compensated for—and strengths cannot be enhanced. Without agrotechnology such as Libelium, decisions are based on assumptions rather than data. Profits may not be maximized, and crops can be diminished or lost.
Integrating Libelium with RoboMQ’s Connect iPaaS enables custom workflow design for timely, data-driven decisions and predictive analytics. IoT sensors monitor growing conditions, detecting humidity, temperature and light. Sensors communicate with the Libelium application, and certain readings trigger events in other applications, such as Slack, PagerDuty, SMS, or actuators. This custom workflow allows for timely response and reaction, optimizing crop management.
Farmers Leverage IoT Technology to Manage Crops and Controls for Climate Challenges
Integrating Libelium with RoboMQ’s Connect iPaaS enables custom workflow design for timely, data-driven decisions and predictive analytics. IoT sensors monitor growing conditions, detecting humidity, temperature and light. Sensors communicate with the Libelium application, and certain readings trigger events in other applications, such as Slack, PagerDuty, SMS, or actuators. This custom workflow allows for timely response and reaction, optimizing crop management.
Transportation Officials Utilize Integrated IoT Technology to for Smart City Parking
Dense commercial and residential traffic in urban areas often creates parking shortages. Drivers wait for coveted spots or drive around waiting for availability, creating congestion. Searching for a parking space wastes time and fuel and increases driver stress and air pollution. A poor parking experience deters return customers.
Providing poor customer parking experience hampers revenue generation, which impacts the tax base. Frustrated customers choose to patronize establishments in areas with ample parking.
Devices with IoT sensors installed on the roadway surface transmit availability data through the Libelium application. Libelium flows information through Connect, which disperses parking availability data to the customer’s preferred application via Connect.
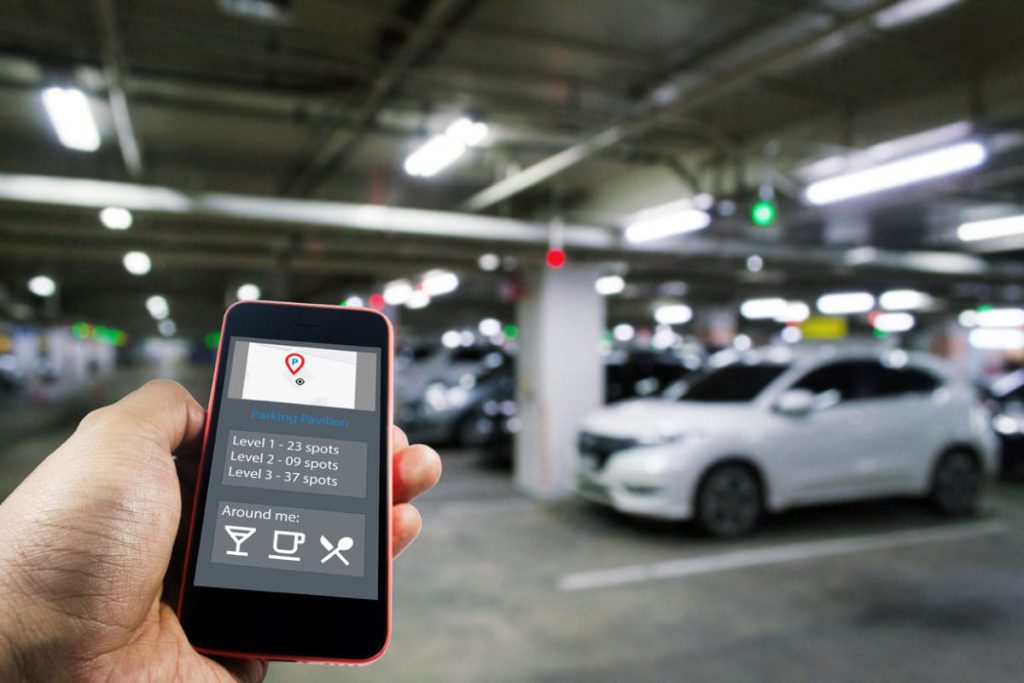
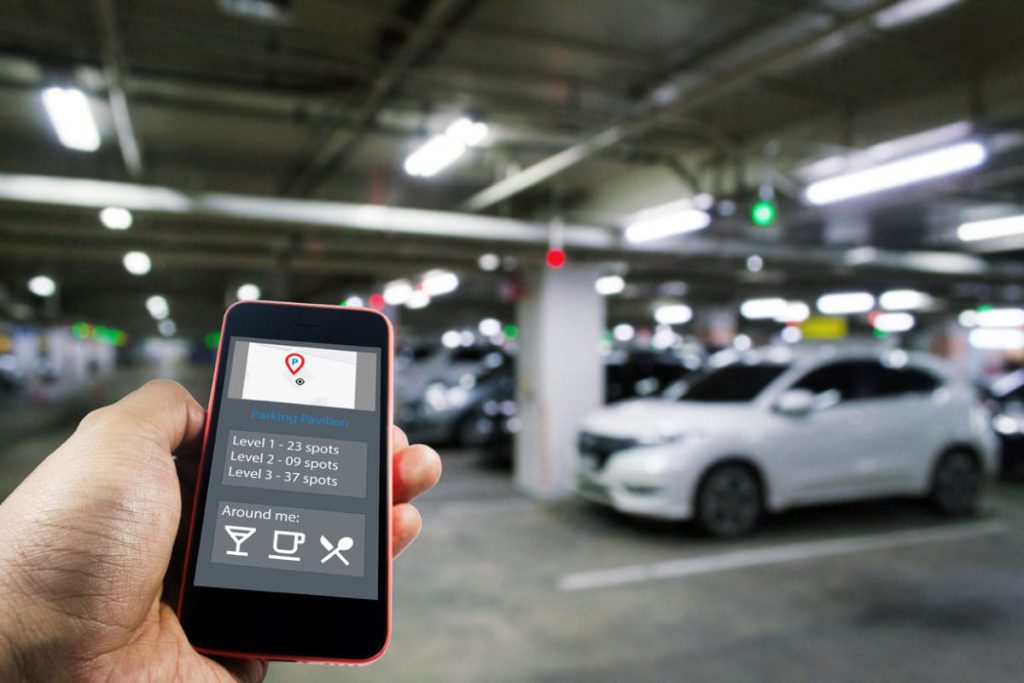
Transportation Officials Utilize Integrated IoT Technology to for Smart City Parking
Providing poor customer parking experience hampers revenue generation, which impacts the tax base. Frustrated customers choose to patronize establishments in areas with ample parking.
Devices with IoT sensors installed on the roadway surface transmit availability data through the Libelium application. Libelium flows information through Connect, which disperses parking availability data to the customer’s preferred application via Connect.
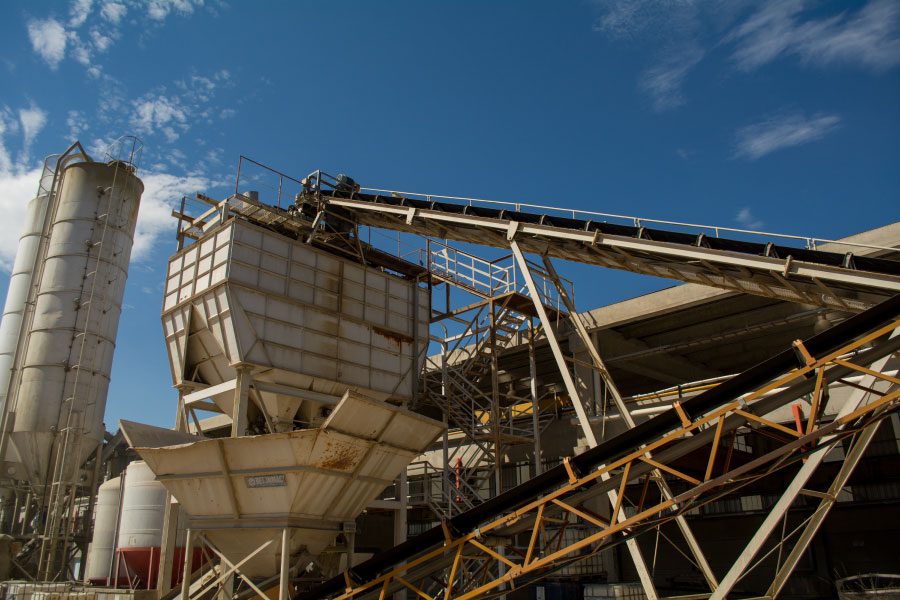
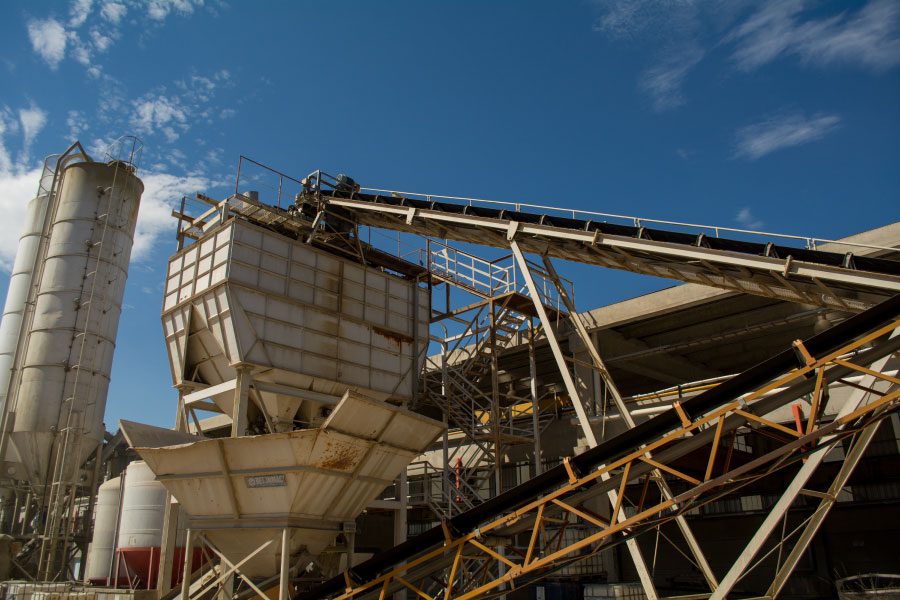
Manufacturing Executives Employ Integrated IoT Strategy for Factory Operations
Manufacturing companies lacked automated processes and relied on employees to notice mechanical failures.
When an element of the production line failed, there lacked a process in place to communicate the change in status, increasing incident response time. Quotas and deadlines were missed, impacting revenue and fulfillment.
Libelium devices with IoT sensors and Connect-based integrations were utilized to monitor physical factory processes. When there is a breakdown or critical change in status, the incident manager receives a message through his or her preferred communication. Real-time and historical data could be analyzed for continuous process improvement, data-driven decision making and proactive manufacturing maintenance. Managers can immediately respond to production line failures and reduce downtime.
Manufacturing Executives Employ Integrated IoT Strategy for Factory Operations
When an element of the production line failed, there lacked a process in place to communicate the change in status, increasing incident response time. Quotas and deadlines were missed, impacting revenue and fulfillment.
Libelium devices with IoT sensors and Connect-based integrations were utilized to monitor physical factory processes. When there is a breakdown or critical change in status, the incident manager receives a message through his or her preferred communication. Real-time and historical data could be analyzed for continuous process improvement, data-driven decision making and proactive manufacturing maintenance. Managers can immediately respond to production line failures and reduce downtime.
Why Choose RoboMQ?
Integrate your business at a price that can't be beat.
Connect your enterprise applications and partner systems to streamline your business.
Create many-to-many event driven API integration flows with SaaS, ERP, CRM and third-party applications.
Leverage the power and scale of cutting-edge technologies like containers and microservices in a simple, intuitive no-code, drag and drop UX.
RoboMQ is not affiliated, associated, authorized, endorsed by, or in any way officially connected with any of the third-party application systems. All product and company names are the registered trademarks of their original owners. The use of any trade name or trademark is for identification and reference purposes only and does not imply any association with the trademark holder of their product brand.
Testimonial
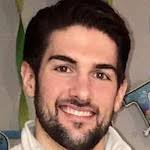
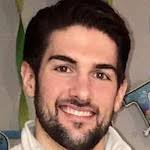